On April 1, Takenori Igarashi, Representative Executive Officer, President & CEO Kawasaki Kisen Kaisha, Ltd. (“K” LINE) made his inaugural speech at its head office.
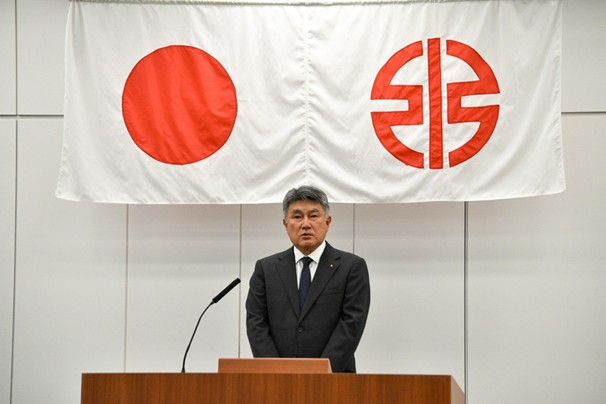
The environment surrounding us is changing at an unprecedented speed. There is the spread of technologies to reduce our environmental impact and the construction of supply chains for the use of new energy as part of decarbonization; the rapid and widespread advance of digital transformation, which includes the use of generative AI; and efforts not only to address the shortage of human resources in various parts of the world, but also to secure diverse human resources and collaborate across industries.
Recently, in addition to the uncertain outlook for geopolitical risks in places such as the Middle East and Ukraine, since the inauguration of the new presidency in the United States this January, uncertainty over global energy and trade policies has also increased. There are moves to introduce policies that could have a major impact on the speed of the shift toward low-carbon and decarbonization, as well as on the supply chain and transportation demand itself, with the raising of customs tariffs on specific countries and products, and the introduction of port entry fees at US ports for ships operated by Chinese shipping companies and ships built in China. The uncertainty of the current business environment outlook is increasing.
Despite these conditions, the “K” LINE Group, under the leadership of former President Yukikazu Myochin, has been steadily advancing a five-year medium-term management plan announced in May 2022, and is bolstering the earnings base of its own businesses, centered on three businesses that will drive growth, by viewing changes such as decarbonization as business opportunities.
In the Coal & Iron Ore Carrier Business, we are working to further strengthen the relationships we have cultivated with customers in Japan, South Korea and China by leveraging customer-oriented and environmental sales. At the same time, we are also working to strengthen relationships with customers in the Indian and Middle Eastern markets, and with major resources companies.
In the Car Carrier Business, we are strengthening our earnings base in a way that meets the needs of our customers by reorganizing our route network, introducing environmentally friendly vessels that achieve low carbon emissions, and increasing the volume of High & Heavy cargo.
In the LNG Carrier Business, in addition to the existing markets of Japan, South Korea, China, and Europe, we are stepping up our efforts in new markets such as Southeast Asia and India, and are on track to expand from our current fleet size of 46 vessels to 65 vessels by fiscal 2026.
Our new business initiatives are also progressing smoothly. The Northern Lights Project in Norway for liquefied CO2 transportation will enter full-scale operation this year, with ship management due to begin for three vessels. In offshore wind power generation support, a Japanese geological survey ship was launched in September of last year, and business development has begun.
We are also working to further strengthen the three functions that form the basis of our strengths (Safety and Ship Quality Management, Advancement of Environmental Technologies, and Digital Transformation), and the human resources and organization that support them. In Safety and Ship Quality Management, we will continue to enhance our safe operation and management system, strengthen our ship management system, and secure and train excellent seafarers to further promote “K” LINE’s top priority of safety in navigation and cargo operations.
In Advancement of Environmental Technologies, we will further integrate our environmental response and technology evolution efforts into a unified strategy, and seek to expand growth opportunities for “K” LINE and society as a whole through low carbon and decarbonization.
In Digital Transformation (DX), we plan to expand and enhance our digital infrastructure by driving DX of data and DX of human resources as defined in our DX Strategy, and to create added value for customers by strengthening our own competitiveness through furthering the digitalization of our own operations and vessels.
I believe that further refining these strengths will support our business in this rapidly changing business environment.
As a logistics company rooted in the shipping industry, “K” LINE’s corporate philosophy is to help make the lives of people more affluent. Working under this philosophy, we operate as a partner that is trusted by all stakeholders, supporting the infrastructure of global society by providing safe, high-quality, optimal services that meet the needs of customers by making thoroughly considered proposals.
For our group to continue achieving sustainable growth in a business environment that is changing at such a dizzying pace, in addition to responding with agility to these changes, we must have the courage and passion to act without fear of change, together with the “animal spirit” needed to boldly take on challenges while calmly assessing risks and opportunities in our corporate activities. Personally, I hope to continue to maintain this attitude, and that everyone in the group will be able to work mindfully toward this. In addition, let’s work to improve the value we provide to all stakeholders and aim to become an even more attractive company.
Finally, I would like to end this message by wishing good health to all of you working within the “K” LINE Group, and to your families.