SAL Renewables acquired both the jack-up vessels Wind Lift I and Thor in 2021 and 2022 and completed a number of projects in and around the waters of northern Europe. Today, the dedicated offshore unit for service, maintenance and installation is taking a new step on its journey: The company is changing its name to Atheleon effective 26 September 2022 in response to the growing importance of wind energy. The Atheleon team is already busy working on an ambitious newbuilding project for the US offshore wind market.
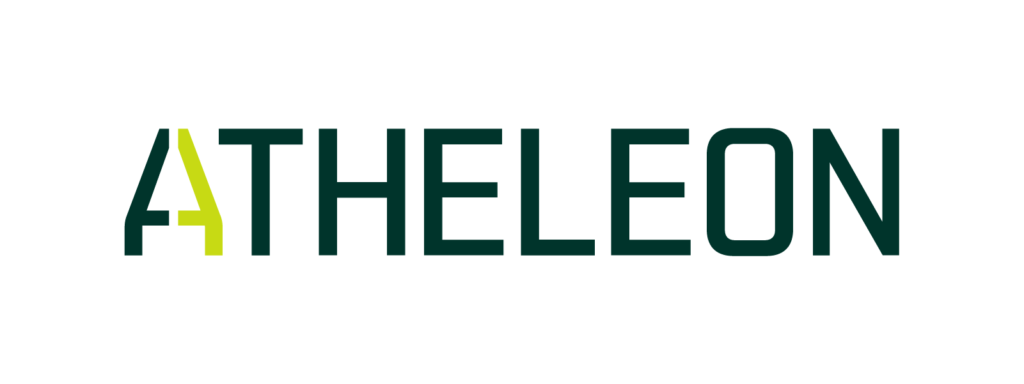
Heiko Felderhoff, Managing Director of the Harren Group and Atheleon, explains: “We see that the time is right to continue our successful journey in the offshore sector under a strong, new and independent name – Atheleon. SAL Heavy Lift holds a leading strategic position within project shipping, and we want to ensure that our customers understand the difference in our service offerings. We realised the brands were too closely associated. Atheleon will continue to represent an epiphany of quality and technical know-how.”
Atheleon is thereby the new go-to market brand for dedicated offshore assignments, especially the renewables sector. Felderhoff: “Atheleon has an exceptional portfolio for its customers: We have a single point of contact for all installation and maintenance services, employ a team of more than 50 engineers and also own all the necessary assets. In addition, we have decades of experience in the offshore industry.”
Atheleon is a unique fictional name inspired by history: the Greek goddess of wisdom Athena and the mythological giant, Leon, who is said to have fought Hercules. “We thought it suited our offshore entity which, while still small in a global context, holds a certain strength in its own right. We utilise the great know-how we have in-house to operate successfully in this sector and see great prospects for Atheleon looking forward,” Heiko Felderhoff continues.
Atheleon will market the offshore jack-up installation vessels Wind Lift I and Thor, together with special vessels such as the Mexican Giant and the VB-10,000. The close cooperation with Wind Multiplikator GmbH and OWS Offshore Wind Solutions GmbH will also continue, unaffected by the name change.
Atheleon also sees immense potential in the US market. “We are working with our partners ONP Management and Renewable Resources Int’l to bring an offshore wind installation concept to the US market,” explains Heiko Felderhoff. “The so-called Feederdock concept will be Jones Act compliant and is a dedicated solution to the rising US offshore transport and installation market.” Feederdock is designed to support the installation of foundation weights of up to 2,800 t and future wind turbine generations with an anticipated capacity of 25 MW and more. It comes with a variety of innovative technical features and follows a strict green design philosophy. Atheleon defined vessel specifications with a crane capacity of 3,000 t and a crane hook height of up to 182 m above deck as key performance criteria. According to Felderhoff: “We are confident that we will be able to bring the ship to market in 2026.”
Harren Group CEO Dr Martin Harren underlines the importance of the renewable energy sector for the entire Group: “Wind energy has become an increasingly important cornerstone of our business in recent years. We are determined to make our contribution to the global energy transition. It’s impossible to overemphasise the importance of the wind market for our Group. Atheleon is the next logical and consistent step to further expanding our commitment in this segment. We offer the renewable energy market a comprehensive range of installation and maintenance services while meeting the highest standards and expectations of these customers.”
About Atheleon: Atheleon is an independent operating offshore company within the Harren Group. The company specialises in offshore maintenance and support services targeted towards the offshore wind sector. Through its access to specialised, diverse and advanced offshore vessels with dynamic positioning and/or jack-up capabilities, Atheleon offers a wide range of expert, cost-efficient services – including vessel time chartering, specialised engineering solutions and complex project management services. Atheleon meets the highest standards with regard to quality, technical innovation, health, safety and environment. Atheleon’s strong global outreach is guaranteed through the large network of Harren Group sales offices and exclusive agents across more than 20 countries. Atheleon has a green perspective and is committed to building a greener tomorrow through its services and technical innovations. For more information about Atheleon, go to www.atheleon.de