Kawasaki Kisen Kaisha, Ltd. (“K” LINE) and Daito Corporation (Daito) have started operating the “Yard Management System” (the system) at the Port of Yokohama Daikoku C-4 Terminal, the first dedicated finished-vehicle terminal in Japan for “K” LINE Group November 2022.
The System manages the status of loading/unloading, vehicle information, and storage locations in the terminal, and its mapping function enables automatic creation of storage maps, making it possible to visualize the status of vehicles more accurately and clearly at a glance. In addition, we aim for efficient yard operations by utilizing the system, such as forecasting the number of vehicles to be stored by accumulating and analyzing past data.
We manage export used vehicles by using QR codes. Also, we can improve the accuracy and efficiency of operations by using handheld equipment, which make us possible to see the status of vehicles quickly and accurately ascertained from anywhere and the latest information can be shared by all parties concerned through the system.
Since the start of operations in April 2022, the terminal has been working to become more environmentally friendly by converting operational vehicles used on the premises to EVs, installing solar carports, and using electricity with virtually zero CO2 emissions from renewable energy sources.
With the introduction of digital technology, the terminal will be able to respond flexibly and proactively to customer needs as a terminal with even higher added value and will strive to always be the preferred choice of customers.
Related Release
May 19th, 2022:“K” LINE Group’s Yokohama Daikoku C-4 Terminal Starts Operation Utilizing Renewable Energy
https://www.kline.co.jp/en/news/terminal/terminal-8056059373266974615/main/0/link/220519EN.pdf
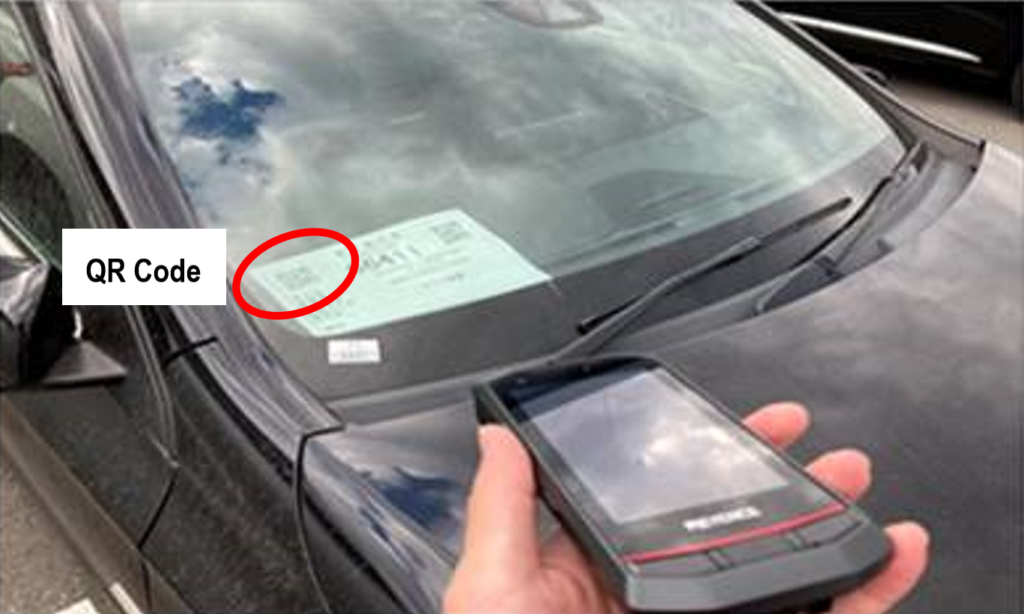
The handheld terminal reads the QR code affixed to the loading table to grasp and register vehicle information.
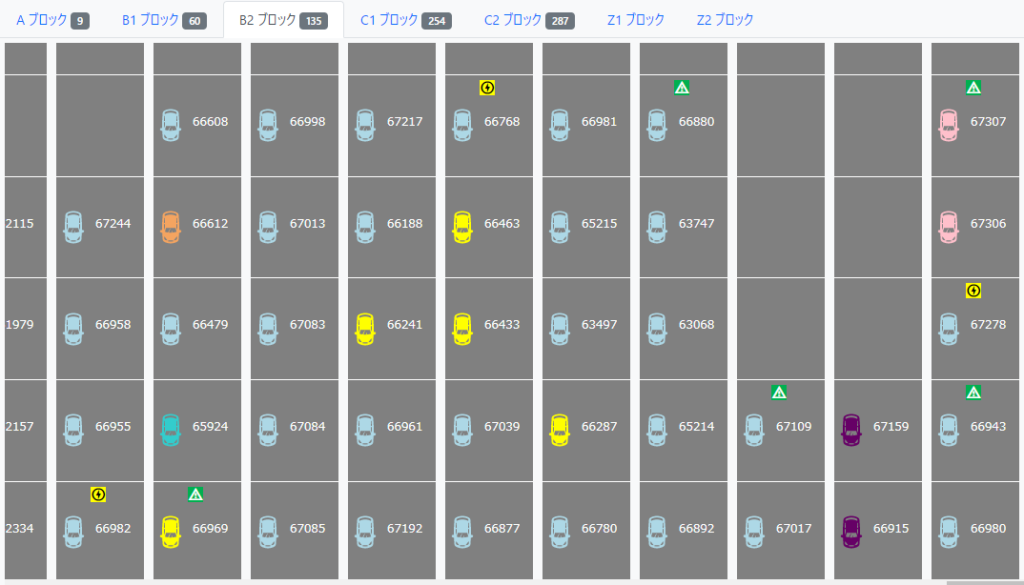
All parties involved can share the latest information for more efficient fleet management.