Kawasaki Kisen Kaisha, Ltd. (“K” LINE) announced today that three “K” LINE Group ship management companies—K Marine Ship Management Pte. Ltd. (KMSM), “K” Line Ship Management (Singapore) Pte. Ltd. (KLSM SGP), and “K” Line LNG Shipping (UK) Ltd. (KLNG UK)—have obtained certification from Nippon Kaiji Kyokai (ClassNK) for the Competency Management System (CMS), a seafarer competency management system being implemented by “K” LINE Group ship management companies. With this system, it will be possible to use it on vessels managed by each company.
The Group’s CMS — which was introduced to facilitate the improvement of seafarer knowledge — not only defines the competency requirements for each seafarer’s position, but also provides specific training and assessment guidelines to achieve those requirements. It includes a variety of training, including onshore training at the “K” Line Maritime Academy training facilities, onboard training programs by auditing and training superintendents*¹ and guidance by senior personnel aboard ship, assessments, and computer-based learning.
The system is operated on the MACK/KONeCT*² digital ship management platforms, custom-designed for KLSM SGP, KLNG UK, and KMSM by SVM Solutions and Technologies Pte. Ltd. (Solverminds). It enables seafarers and onshore staff to seamlessly access their training requirements online, from either aboard ship or ashore, via their platform’s training portal.
Through the use of this system, we clarify the required competencies and aim for the following,
- For career advancement both at sea and on land
- To provide equal opportunities regardless of nationality
- To ensure that the right personnel are assigned to the right positions at the right time.
We aim at a safe and comfortable environment where onshore and offshore personnel with diverse values and different nationality, gender can make full use of their skills.
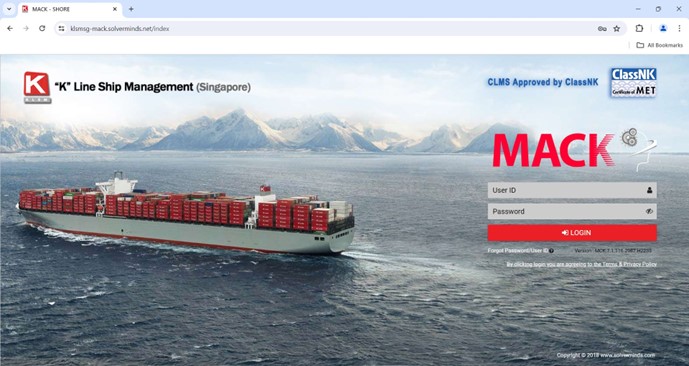
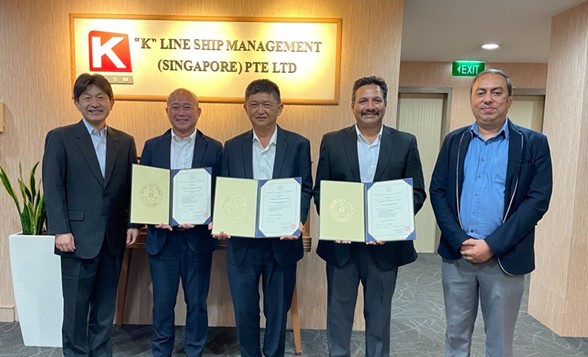
From left:
Naoki Saito, General Manager, Maritime Technology Department, Business Development Division, ClassNK
Akihiro Fujimaru, Managing Executive Officer of “K” LINE and CEO of K LINE MARINE & ENERGY PTE. LTD.
Capt. Takafumi Tomaru, Managing Director, KLSM SGP
Capt.Rajan Mathur, General Manager, Training, Audit and Competence Management Group, KLSM SGP
Capt.Ritesh Sood, Managing Director, Solverminds
*1. Auditing and training superintendents
Former “K” LINE Group captains or chief engineers, stationed aboard vessels managed by the Group for a certain period of time to provide on-board training and supervision for other seafarers aboard ship.
*2. MACK/KONeCT
Ship management system platforms. MACK is used by KLSM SGP, and KONeECT is used by KMSM. These platforms have many functions serving as integrated solutions, such as a safety control system and safety and quality control, ship inspection management, scheduled maintenance, procurement and training functions.