The France 2023 Organising Committee has announced that GEODIS, a global leading transport and logistics provider, has been appointed as Official Fret Carrier of the tournament. GEODIS has therefore committed to provide bespoke logistics services with the target of having the lowest possible impact on the environment.
Drawing on its expertise, worldwide capabilities and infrastructure, GEODIS will be responsible for ensuring the efficient management of approximately 80 tons of equipment for the 20 participating nations. It will also meet the logistical needs of the thousands of volunteers involved throughout the tournament. GEODIS will be fully dedicated to the seamless delivery of this major international sporting event, across nine stadiums in 10 French host cities.
In accordance with the Group’s ambition to continuously reduce its CO2 emissions by 2030, GEODIS will use low-carbon vehicles to achieve its mission. GEODIS is already committed to deploying such fleets in roughly 40 French cities between now and 2024.
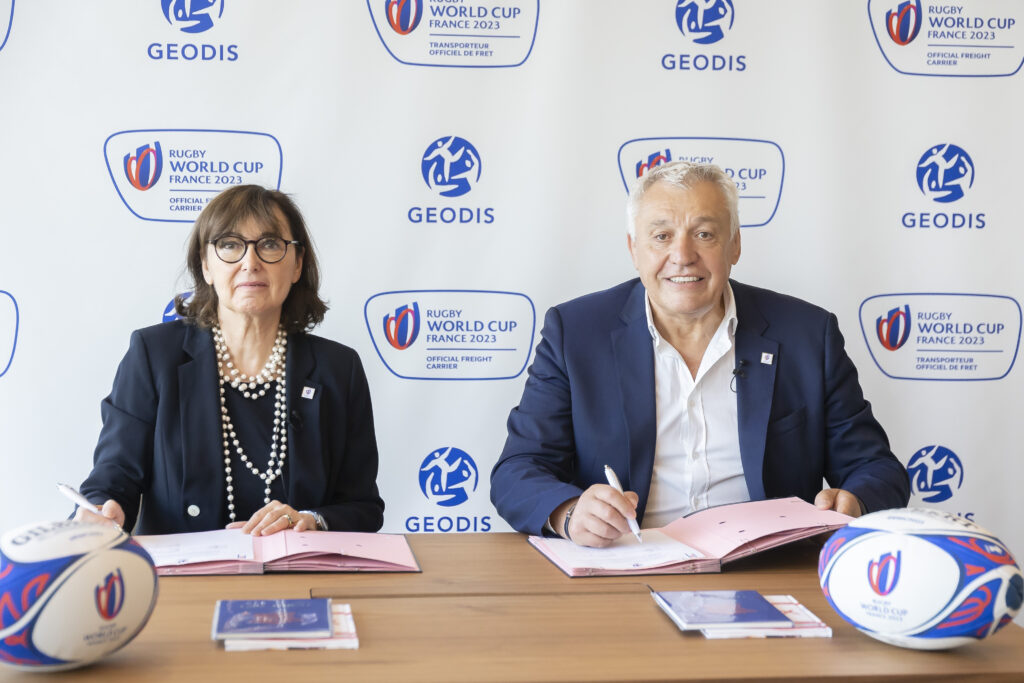
Claude Atcher, France 2023 CEO, said: “From the start of the France 2023 project, we made our responsibility clear: to organise an event capable of minimising its impact on the environment, notably through the help of its partners. We are happy to share this ambition with GEODIS, a company that is both experienced in delivering international sporting events and committed to tackling environmental issues within its industry. We will work together to make Rugby World Cup 2023 a sustainable event, aligned with societal challenges of today and tomorrow.”
Marie-Christine Lombard, GEODIS CEO, said: “I am proud that GEODIS has been entrusted with the critical mission of being the Official Freight Carrier of Rugby World Cup France 2023. Team spirit, integrity, passion, discipline and respect are all values that characterise this sport and that we share at GEODIS. As the CEO of a French-rooted yet truly international group, I am excited for our teams to play a part in an event that brings so many people together and that gives France the opportunity to shine at an international level.”
ABOUT RUGBY WORLD CUP FRANCE 2023:
Rugby World Cup 2023 will take place in France from 8 September-28 October with matches played in nine venues across 10 host cities. The tournament will be the 10th men’s Rugby World Cup and the second to be hosted by France after a memorable event in 2007.
RWC 2023 will take place in a year when the sport celebrates 200 years since Rugby School pupil William Webb Ellis was credited with inventing the game of rugby football by showing “a fine disregard for the rules” in catching the ball and running with it in 1823.
RWC 2023 will set new standards in social responsibility, inclusion and sustainability for a major rugby event, targeting four key pillars for the tournament’s legacy: acting for sustainability and circular economy, supporting education, training and employment, respecting and protecting the environment and promoting inclusivity by being a champion for gender equality.
The showpiece event in men’s 15s, Rugby World Cup 2023 will feature 20 teams – 12 of whom qualified directly by finishing in the top three in their pool at Japan 2019 and eight from a global qualification process – with 48 matches played across 51 days.
ABOUT GEODIS:
GEODIS is a global leading transport and logistics provider recognized for its commitment to help clients overcome their logistical constraints. GEODIS’ growth-focused offerings (Supply Chain Optimisation, Freight Forwarding, Contract Logistics, Distribution & Express, and Road Transport), coupled with the company’s truly global reach thanks to a global network spanning nearly 170 countries, is reflected in its top business rankings: no. 1 in France and no. 7 worldwide. GEODIS employs more than 44,000 people globally and has generated €10.9 billion in revenue in 2021.
More information on Geodis: www.geodis.com