“K” Line Ship Management (Singapore) Pte Ltd (KLSM SGP), a group company of Kawasaki Kisen Kaisha, Ltd (“K” Line), was certified by ClassNK for Cyber Security Management System (CSMS) recently after CSMS acquisition of “K” Line Energy Ship Management Co., Ltd.,Tokyo. (Note 1)
The ship management companies in “K” Line group are not only targeting to acquire the CSMS certification but have been working on the development of practical measures and guide to safely protect ships from Cyber Security threats as first priority. KLSM SGP has been incorporated Cyber Security Management into Safety Management System (SMS) manual and developed Cyber Security Management Plan (CSMP) and its guide (CSMG) as supplementary volume, and KLSM SGP and container ship “ONE HAMBURG” managed by KLSM SGP acquired CSMS certification.
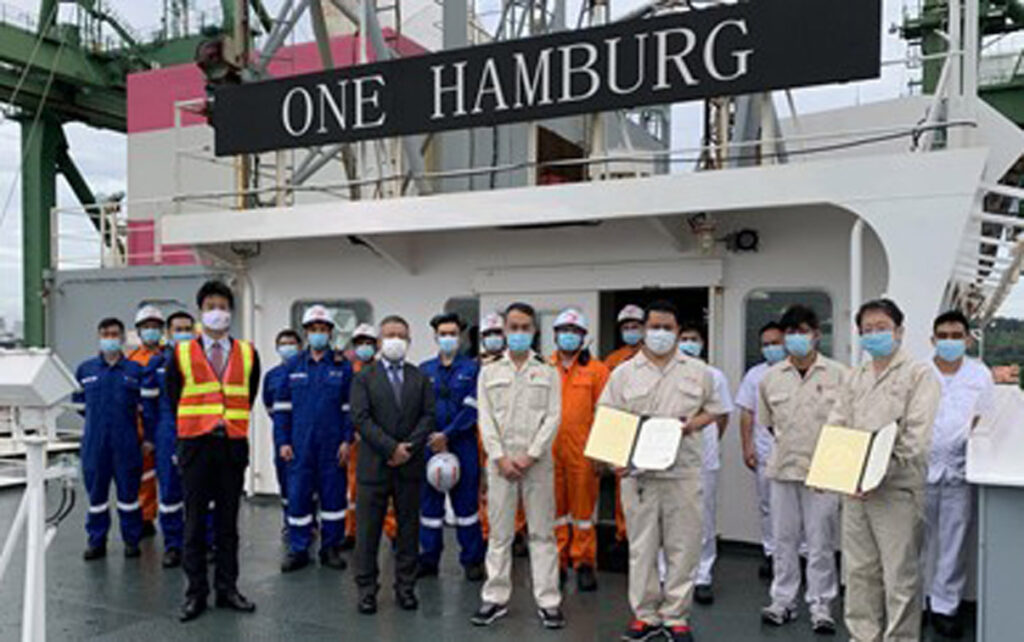
KLSM SGP prepared under the various restrictions imposed by COVID-19, and the certification process by ClassNK was completed on October 15, 2020. All vessels under the management of KLSM SGP will be equipped with required IT equipment and arrangements for Cyber Security measures in accordance withy the certified guide in the same manner as “ONE HAMBURG”.
We will provide the safer and best maritime transport service by strengthening protection against cyber risks on both shore and ships.