“K” Line Wind Service, Ltd., a joint venture company between Kawasaki Kisen Kaisha, Ltd. (“K” LINE) and Kawasaki Kinkai Kisen Kaisha, Ltd. (*1), is granted for Class C Innovation Endorsement Provider Certification for organizations by ClassNK.
ClassNK offers its third-party Innovation Endorsement “Provider Certification”, which supports innovative initiatives, to companies and organizations. As companies pursue ESG-oriented management and SDGs, ClassNK conducts the third-party certification on the initiatives to transform their own business methods and organizations in order to establish the sustainable and competitive business. There are three categories of certification available to companies according to their innovation activity stage. (*2)
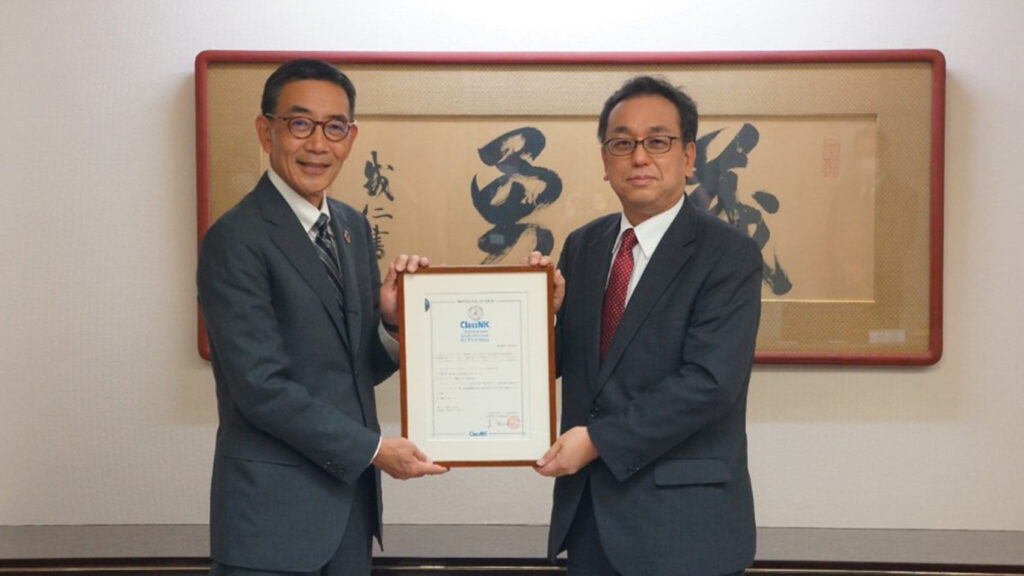
Offshore Wind development is recognized as one of the most important items for Japan to reach carbon neutrality by 2050 and in order to contribute to its development in Japanese ocean, “K” Line Wind Service has been established as a business platform of “K” Line group for any vessel and transportation business around Offshore Wind projects in Japan.
“K” Line Wind Service is established with mission to contribute to the development of offshore wind as well as marine industry in Japan through the activities such as the program of “Mass-production and Cost Reduction of Floating Offshore Wind Installation” adopted by Green Innovation Fund run by NEDO. (*3)
“K” Line Wind Service will continuously explore the new and competitive solutions in Japanese Offshore Wind projects while pursuing SDGs.
(*1) “K” Line Wind Service, Ltd
A joint venture company established by Kawasaki Kisen Kaisha, Ltd. and Kawasaki Kinkai Kisen Kaisha, Ltd. on June 1st, 2021 targeting the contribution to Offshore Wind in Japan throughout the marine solution that the group have developed in the history of 100-year.
Announcement on April 30th, 2021:
Establishment of “K” Line Wind Service, Ltd. for Offshore Support Vessel Operation
(https://www.kline.co.jp/en/news/energy/energy1216843343315336832/main/0/link/210430EN2.pdf)
(*2) Innovation Endorsement by ClassNK
ClassNK started to offer its third-party Innovation Endorsement in 2020, which supports innovation initiatives, to companies and organizations. There are three categories (1) Notation, (2) Product & solutions certification, and (3) Provider certification with three categories of certification available to companies according to their innovation activity stage.
Class C (Concept: Organizational policy and system in place for innovation)
Class D (Development: Specific innovation activities being carried out)
Class S (Sustainable Implementation: Sustainable innovation with results implemented in the business)
https://www.classnk.or.jp/hp/en/activities/techservices/dgd2030/iea/index.html
(*3) “Mass-production and Cost Reduction of Floating Offshore Wind Installation” adopted by Green Innovation Fund run by NEDO
“K” Line Wind Service, Ltd., a joint venture company between Kawasaki Kisen Kaisha, Ltd. (“K” LINE) and Kawasaki Kinkai Kisen Kaisha, Ltd. (*1), together with Japan Marine United Corporation, Nihon Shipyard Co., Ltd. and Toa Corporation is pleased to announce that the project of “Mass-Production and Cost Reduction of Floating Offshore Wind Installation” was officially adopted as Green Innovation Fund for “Cost Reduction for Offshore Wind Power Generation Projects”
Announcement on January 21st, 2022:
Joint project on “Mass-production and Cost Reduction of Floating Offshore Wind Installation” adopted as Green Innovation Fund
https://www.kline.co.jp/en/news/energy/energy-7251549612202879904/main/0/link/220121EN.pdf